Do it yourself knobs
ID: 128525
Do it yourself knobs
20.Dec.06 04:01
0
Do it yourself knobs.
Start with a set of good knobs. Or, take what's left of the old knobs and glue them together, fill in with lacquer putty and make look like they are supposed to.
Mount the knobs to a flat plate of plexiglass. Note: some of the knobs may require holes drilled in the plexiglass to hold shoulders, shaft extensions etc.. I use 1/2" (12mm) double stick tape to hold the knobs to the plexiglass bottom plate.
Stick a few #10 (4mm) hex nuts to the base plate to use as alignment keys in the mold.
Use 1/16" (1.6mm) styrene and make a form for the mold. Make it deeper than the exposed portion of the knobs.
Drill 5/16" (8mm) holes in the sides of the form to hold set-screw fillers made from brass rod.
In my case, I turned them to 0.065" (#36 drill) and 0.145" (#28 drill) to account for 6-32 set screws. After inserting the set screw shafts in to knobs through the side of the form, set them in place with some hot melt glue. Glue the corners of the form together with holt melt glue as well, and to the plexiglass base plate.
Give the knobs and inside of the mold a light coating with mold release. Mix the silicon elastomer and pour SLOWLY into the mold. Use a dental pick to chase the bubbles up to the surface of the pour. Note: I am using 2-part (90% silicon, 10% hardener) RTV silicon elastomer. It is available from Dow Corning.
Let cure overnight. The next morning, put in a warm oven, about 125 degrees F (50 C) and do a final cure for 20-30 minutes.
DO NOT REMOVE KNOBS FROM THE MOLD YET.
Remove the hex nuts from the mold.
Take the original frame (mold) apart by removing the hot melt glue. I find that a little bit of turpentine causes the hot melt glue to let go and remove eaisily.
Make a new mold frame out of styrene around the original mold. Treat the silicon surface with vasolene. (Use a small paint brush and coat all exposed surfaces of the first silicon mold that will have fresh silicon poured against it.
Use turned rods of the appropriate size for the shaft holes in the back of the knobs.
Give the mold interior and exposed knob backs a light coating of mold release.
Mix up another batch of silicon elastomer and pour slowly into the mold. Again, chase the bubbles up to the surface with a small curved dental pick.
Let set over night and again do a final cure of 20-30 minutes at 125 F (50 C).
You're almost ready to make knobs now.
Use a piece of small diameter brass tubing, .125" (3mm) with the INSIDE edge chamfered to use a drill to cut spru holes in the mold. This allows excess material to flow out of the mold in a predicatable fashion.
I cut my holes in the back side mold so that the excess casting material doesn't show on the front of the knobs.
Spray both mold pieces with a light coating of mold release.
Mix the casting material an pour some into the first mold almost full. Dribble a little bit into the mating mold to pre-coat the inner surfaces. Press the two mold halves together. Watch the excess material come up through the top spru holes. I am using 2-part (50%-50%) rigid casting urethane. 90-110 shore (hardness). In it's natural state, it's kind of a horrible yellow-cream color. You can use the dies specified by the manufacturer to make it any color you want. To make swirl patterns, mix two batches of urethane, say brown and cream, them swirl together prior to pouring in the mold.
Wait about 5 minutes and use a putty knife to move the excess casting material from the top of the spru holes.
Walk away and find something else to do for the next 20-30 minutes.
Gently seperate the two mold pieces. pay close attention to the part with the spru holes in it, as that requires a bit of dexterity to pry off of the part without damaging the mold.
Trim the excess material off of the new knobs.
By hand, run the required size drill bits into the set secrew holes to ensure they are the correct size, then use a tap to shread the smaller diameter.
And now, as if by magic, you have a fresh new duplicate set of knobs for that radio you've been wondering where to find knobs for.
Jeff Angus
Stay Connected
Attachments:
Start with a set of good knobs. Or, take what's left of the old knobs and glue them together, fill in with lacquer putty and make look like they are supposed to.
Mount the knobs to a flat plate of plexiglass. Note: some of the knobs may require holes drilled in the plexiglass to hold shoulders, shaft extensions etc.. I use 1/2" (12mm) double stick tape to hold the knobs to the plexiglass bottom plate.
Stick a few #10 (4mm) hex nuts to the base plate to use as alignment keys in the mold.
Use 1/16" (1.6mm) styrene and make a form for the mold. Make it deeper than the exposed portion of the knobs.
Drill 5/16" (8mm) holes in the sides of the form to hold set-screw fillers made from brass rod.
In my case, I turned them to 0.065" (#36 drill) and 0.145" (#28 drill) to account for 6-32 set screws. After inserting the set screw shafts in to knobs through the side of the form, set them in place with some hot melt glue. Glue the corners of the form together with holt melt glue as well, and to the plexiglass base plate.
Give the knobs and inside of the mold a light coating with mold release. Mix the silicon elastomer and pour SLOWLY into the mold. Use a dental pick to chase the bubbles up to the surface of the pour. Note: I am using 2-part (90% silicon, 10% hardener) RTV silicon elastomer. It is available from Dow Corning.
Let cure overnight. The next morning, put in a warm oven, about 125 degrees F (50 C) and do a final cure for 20-30 minutes.
DO NOT REMOVE KNOBS FROM THE MOLD YET.
Remove the hex nuts from the mold.
Take the original frame (mold) apart by removing the hot melt glue. I find that a little bit of turpentine causes the hot melt glue to let go and remove eaisily.
Make a new mold frame out of styrene around the original mold. Treat the silicon surface with vasolene. (Use a small paint brush and coat all exposed surfaces of the first silicon mold that will have fresh silicon poured against it.
Use turned rods of the appropriate size for the shaft holes in the back of the knobs.
Give the mold interior and exposed knob backs a light coating of mold release.
Mix up another batch of silicon elastomer and pour slowly into the mold. Again, chase the bubbles up to the surface with a small curved dental pick.
Let set over night and again do a final cure of 20-30 minutes at 125 F (50 C).
You're almost ready to make knobs now.
Use a piece of small diameter brass tubing, .125" (3mm) with the INSIDE edge chamfered to use a drill to cut spru holes in the mold. This allows excess material to flow out of the mold in a predicatable fashion.
I cut my holes in the back side mold so that the excess casting material doesn't show on the front of the knobs.
Spray both mold pieces with a light coating of mold release.
Mix the casting material an pour some into the first mold almost full. Dribble a little bit into the mating mold to pre-coat the inner surfaces. Press the two mold halves together. Watch the excess material come up through the top spru holes. I am using 2-part (50%-50%) rigid casting urethane. 90-110 shore (hardness). In it's natural state, it's kind of a horrible yellow-cream color. You can use the dies specified by the manufacturer to make it any color you want. To make swirl patterns, mix two batches of urethane, say brown and cream, them swirl together prior to pouring in the mold.
Wait about 5 minutes and use a putty knife to move the excess casting material from the top of the spru holes.
Walk away and find something else to do for the next 20-30 minutes.
Gently seperate the two mold pieces. pay close attention to the part with the spru holes in it, as that requires a bit of dexterity to pry off of the part without damaging the mold.
Trim the excess material off of the new knobs.
By hand, run the required size drill bits into the set secrew holes to ensure they are the correct size, then use a tap to shread the smaller diameter.
And now, as if by magic, you have a fresh new duplicate set of knobs for that radio you've been wondering where to find knobs for.
Jeff Angus
Stay Connected
Attachments:
- Original and newly cast knobs (87 KB)
- Front and back mold patterns (76 KB)
- Side view of molds (74 KB)
To thank the Author because you find the post helpful or well done.
21.Dec.06 06:17
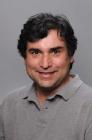
Jeff,
Out of curiosity, what are the main issues with vintage American radio knobs, that they would need replicating?
For some reason, the the pre and post war German radio knobs seem to be in pretty good shape, save, for occasional hairline stress fractures.
To thank the Author because you find the post helpful or well done.
24.Dec.06 21:51
Omer wrote: Out of curiosity, what are the main issues with vintage American radio knobs, that they would need replicating?
Several things come to mind. First off, missing. A replacement knob is always better than a bare shaft sticking out of a front panel. Secondly, damaged knobs. These fall into two categories. Natural causes, such as shrinkage or the plastic degrading over time and crumbling. Some pre-war Philco radios suffer this fate. The knob ends up looking like three week old corn bread. And of course, knobs that break in the process of trying to remove them from a shaft. Typically, the set screw ends up frozen to the knob or the insert. And then there's the third reason. Theft.
By the way, in reference to my previoius posting, these are the materials I'm using for making knobs.
Ax-Sil 4240 Resin "Mold making silicone elastomer" and Burman Industries TC-810 "Rigid Urethane".
Jeff
Several things come to mind. First off, missing. A replacement knob is always better than a bare shaft sticking out of a front panel. Secondly, damaged knobs. These fall into two categories. Natural causes, such as shrinkage or the plastic degrading over time and crumbling. Some pre-war Philco radios suffer this fate. The knob ends up looking like three week old corn bread. And of course, knobs that break in the process of trying to remove them from a shaft. Typically, the set screw ends up frozen to the knob or the insert. And then there's the third reason. Theft.
By the way, in reference to my previoius posting, these are the materials I'm using for making knobs.
Ax-Sil 4240 Resin "Mold making silicone elastomer" and Burman Industries TC-810 "Rigid Urethane".
Jeff
To thank the Author because you find the post helpful or well done.
04.Jan.07 23:44
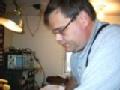
Jeff,
Have you used this method for Bezels and escucheons? I have a Philco and an RCA console that have no reproduction Bezels available.
Paul.
To thank the Author because you find the post helpful or well done.
06.Jan.07 05:37
A very simple technique for making a "one of" pattern is to use modeling clay. Spray the escutcheon with mold release (or use something like Pam spray cooking oil) and press the clay onto the part you want to duplicate. Add addition bits of clay to make it the same height all the way around as it needs to sit level once you turn it over. Remove the part and do any touch ups that might be necessary with an orange-wood stick. These are like large toothpicks available in the fingernail care section for women. Pointed at one end and flat chisled on the other. Mix up a batch of casting urethane as mentioned above and pour into the pattern mold you just made.
The advantage of this method is that modeling clay is a LOT cheaper than silicon elastomer. And, you can "adjust" the clay a little bit to straighten out warped escutcheons if necessary. Once you make a "good" one, then you can use the silicon to make mold off of the corrected pattern.
You can also touch up the cast part with bondo or lacquer putty to fix any other little imperfections before making an expensive silicon mold. Or just use your "fixed" casting as the finish part if that's the only one you needed.
Jeff
The advantage of this method is that modeling clay is a LOT cheaper than silicon elastomer. And, you can "adjust" the clay a little bit to straighten out warped escutcheons if necessary. Once you make a "good" one, then you can use the silicon to make mold off of the corrected pattern.
You can also touch up the cast part with bondo or lacquer putty to fix any other little imperfections before making an expensive silicon mold. Or just use your "fixed" casting as the finish part if that's the only one you needed.
Jeff
To thank the Author because you find the post helpful or well done.