schräge RES964 -Qualitätsaufwendungen eines Rö.Herstellers
ID: 178740
Dieser Artikel betrifft das Bauteil: Zur Röhre/Halbleiter
schräge RES964 -Qualitätsaufwendungen eines Rö.Herstellers
08.Dec.08 01:04
5194
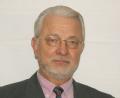
Aufwendungen eines Röhrenherstellers zur Fertigung langzeit zuverlässiger Röhren
>Teil1:Sichtweise Röhrenhersteller<
Teil 2 behandelt die Thematik aus Sicht des Anwenders
I. Konstruktion
Gewähr zuverlässige und qualitativ beste Röhren zu entwickeln und in Serienfertigung herzustellen, bedurfte von jeher einer Reihe grundlegender technischer und finanzieller Anstrengungen. Dies betraf abhängig der gestellten elektrischen Anforderungen im Wesent-lichen die Konstruktion, die Materialwahl und deren Verwendungen, die Einzelteile-fertigung, die Montagepräzision sowie die Prüfaufwendungen während der Fertigung und im Qualitäts-Kontroll-Bereich. Es bedurfte vor Beginn einer Neuentwicklung und Fertigung u.a. umfassender Messungen und Untersuchungen bisheriger Röhrentypen, anhand derer Verbesserung festgelegt bzw. analysierte typische Fehlerquellen korrigiert wurden. Fach-ingenieure der Entwicklungs- und Versuchsabteilungen, der Fertigung und der Qualitäts-kontrolle haben dazu in der Vergangenheit folgende Mängel-Hauptfaktoren analysiert, die es zu berücksichtigen galt, wie:
a. Herabsetzung der Anzahl von Schweißstellen.
b. Verkürzung des Systemaufbaus mit Verwendung größerer Katodendurchmesser.
c. Enge Lochausstanzungen für die Durchführung mit festem Sitz der Gitterstege mit optimierten doppelten Glimmerhülsen.
d. Zur besseren Halterung der Gitter sperrende Bänder in den Glimmerteilen.
e. Für den Röhrenfuß Festlegung der unteren Glimmerteile an mehreren Stellen.
f. Festlegung der Anode an den Glimmerteilen durch über die Anodenlappen geschweißte Bänder, statt Umbörtelung oder Verdrehen der Anodenlappen.
g. Konstruktive Maßnahmen, die den Anoden eine größere Steifigkeit und einen festeren Sitz geben.
Aus diesen Erwägungen heraus sind beispielsweise alle Systeme der Langlebensdauer-röhren kurz und robust aufgebaut, d.h., mit kastenförmig ausgebildeten Anoden, kurzen Zuleitungslängen und durch Stützglimmer fest gehalten, werden die Röhren in einem "kalibrierten" Kolben zu starren Einheiten. So ist das System der E180F z.B. nur 6,5mm lang und mit sehr kurzen Zuleitungen auf dem Sockel montiert.
II. Material
Der intensive Aufwand, der für eine erhöhte Zuverlässigkeit der Langenlebensdauerröhren notwendig ist, begann bereits mit der Auswahl und Bereitstellung der Rohmaterialien. Eine erste Forderung war dabei vor allem die Reinheit des Rohmaterials, da hiervon weitest-gehend die Katodenaktivität, die Isolation, die Geräuschfreiheit und das Vakuum der Röhren abhängen.
1. Katodenmaterial
Für die meisten Langlebensdauerröhren verwendete man, um die Neigung zur Zwischen-schichtbildung gering zu halten, aktives Nickel mit wenig Silizium und Magnesium. So kam z.B. für die Röhren E90CC und die E92CC mit zwischenschichtfreier Spezialkatode, die einst für Rechenmaschinen entwickelt wurden, spezielles passives Nickel zum Einsatz, das praktisch frei von Magnesium und Siliziumbeimengungen ist.
2. Glas * siehe auch Seiten 166-1 / -2 und 353 bis 359
Eines der wichtigsten Röhrenwerkstoffe stellte Glas dar. Es hat den Vorteil der Durchsichtig-keit, der chemischen Unangreifbarkeit, der elektrischen Isolation, der Festigkeit und der Möglichkeit, es in der Flamme schmelzen zu können. Dagegen ist es spröder als ein dichtes Material und erfordert im technischen Prozess, um eine genügende Bruchsicherheit sicher zu stellen, einige Ver-feinerungen. Als erstes bedurfte es der Einhaltung der Röhrenkolben-Wandstärken u. -Abmessungen, normativ durch den Ausdehnungskoeffizienten Ö
des jeweils verwendeten Glases bestimmt. Für den Fuß setzte man daher meist ein Bleiglas und für den Kolben ein Kalk-Naturglas ein, wodurch der Fuß durch den Kolben etwas gedrückt wurde. Über günstige oder ungünstige Verbindungen der verschiedenen handelsüblichen Gläser gibt eine Tabelle Auskunft, gelistet in"Proceedings of the I-R-E Band 40, Nr.10, Okt. 1952, Seite 1166".
* siehe Beitragsende: Beschreibung einer Messmethode zur Bestimmung des a-Wertes
Ö Ist für das Fußglas eine besonders wichtige Größe,weil er sich wegen der metallischen
Durchführungen nur in kleinen Grenzen ändern darf. Weitere wichtige Glaseigenschaften
sind deren Viskosität und Isolations widerstand. Auch diese beiden Größen werden
bei Materialeingang kontrolliert, gemessen.
3. Kontrolle
Für die angelieferten Rohmaterialien bestand die feste Vorgabe, diese laufend durch quantitative physikalische und chemische Messmethoden zu überwachen. Als erstes war gefordert, die vorgegebenen Toleranzen einzuhalten, alle Materialien zu 100% auf Maßhaltigkeit zu kontrollieren und mechanisch technologisch zu prüfen, wie z.B. die Biege- und Zerreißfestigkeit von Drähten, von Blechen, ganzen Systembauteilen, sowie auf Glas bezogen einigen mechanischen Prüfungen besonderer Art.
Weiterhin mussten die ausgewählten Rohmaterialien bzw. Halbzeuge oder Einzelteile ähnlich wie chirurgische Instrumente gründlichst durch Waschen, Kochen und Entfetten gereinigt und die Oxidüberzüge an Metallen durch Reduktion unter Schutzgas entfernt werden. Die Verwendung zahlreicher Hilfsstoffe, Reinigungsmittel für die Stanzteile wie (Tri -Trichloräthylen oder Per -Perchloräthylen), das Wasser, sowie Spül- und Brenngas unterlagen ebenfalls einer strenger Prüfung mit laufender Analyse, um nicht mit Spuren vorhandener unzulässiger Beimengungen die Katodenemission frühzeitig zu vergiften. Für die Chemikalienherstellung der Emissionspaste waren zur Feststellung schädlicher Beimengungen chemische und spektrolytische Untersuchungen besonders wichtig: Als weitere erforder-liche Messmethoden waren zu berücksichtigen:
a. spektrografische Untersuchungen des Katodenmaterials
b. die Prüfung der Getteraktivität
c. eine Gasabgabemessung an den Metallen der Elektrodensysteme
Die Katodenwerkstoffe für Röhren mit hoher Lebensdauer bedurften besonderer Reinheits-anforderungen, die im zeitlichen Ablauf der Röhrenentwicklung immer bedeutsamer und dank verfeinerter Messverfahren sich realisieren ließen. So bot die Spektralanalyse für die laufende Überwachung ein rasch durchzuführendes Verfahren. Es ermöglichte noch Bei-mengungen von etwa 0,05% sicher zu erfassen, bzw. abhängig vom nachzuweisenden Stoff noch Beweise bis zu 0,001…0,0001% zu erbringen.
So war zur Vermeidung einer widerstandsbehafteten Zwischenschicht in den Katoden eine genaue Überwachung des Katodennickels von besonderer Signifikanz. Alle übrigen Röhren-werkstoffe, wie Nickel- oder Eisenbleche waren in vergleichbarer Weise auf Verunreini-gungen zu prüfen. Auch leicht flüchtige Beimengungen von Zink oder Kadmium konnten durch diese Prüfung erkannt und ausgeschieden werden. Diese Verunreinigungen, die sichauf den Gläsern, den Glimmerscheiben oder Elektroden niederzuschlagen neigten, waren neuralgische Schwachstellen für mögliche spätere Isolationsfehler und Krachstörungen. Alle vorgenannten Material Prüf- und Kontrollmaßnahmen waren jedoch nutzlos, wenn keine Vorkehrungen gegen nachträglich erneute Verunreinigungen getroffen wurden.
Als weiteres wichtiges Bauelement gehörte der zur Stromzuführung benutzte Sockelstift-draht [Finkh], denn er ist mit verantwortlich für die Aufrechterhaltung des Vakuums. Durch ständige Überwachungen in Rissprüfgeräten und durch Anfertigung von Querschliffen war zu überwachen, dass er keine Kanäle aufwies, durch die im Laufe der langen Lebensdauer möglicherweise Luft in die Röhre eindringen könnte. So ist z. B. ein Kanal von 0,01mm lichter Weite ohne starke Vergrößerung kaum zu erkennen. Eine Röhre mit dieser Draht-qualität würde aber frühzeitig ausfallen. Wegen dieser Problematik wurden die Drähte vor Verwendung gerollt und so die feinen Risse eingeglättet.
Auch das Glasverhalten bei hohen Temperaturen musste explizit geprüft werden, da es im Laufe des Fertigungsprozesses wiederholt erhitzt, geschmolzen bzw. mit Metallen ver-schmolzen und wieder abkühlte. Die hierzu erforderlichen Messungen der Wärmeausdehnung ließen sich abhängig von der Glasart, von Zimmertemperatur, bis zu einem Erweichungs-punkt von 480- 600°C zurückführen. Angesichts spezieller Glaseigenschaften, bei Zug- oder Druckspannung doppelbrechend zu werden, kam hierfür als genauere Messmethode die Polarisationsmikroskopie in Anwendung. Unter dem Polarisationsmikroskop ließ sich aus dem Grad der optischen Veränderungen des Glases unmittelbar die Höhe der Spannung bestimmen.
III. Teilefertigung
1. Allgemein
Die hohen Anforderungen, die an Langlebensdauerröhren gestellt werden, machten es erforderlich, die Einzelteilefertigung auf speziell für diese Röhrentypen konstruierten Präzisionsmaschinen vorzunehmen. So empfahl es sich, die Bauteile nicht fortlaufend, sondern nur im Umfang einer Tagesproduktion herzustellen, ein einfaches Vorgehen, um Verunreinigungen zu begrenzen.
Als weitere Vorbeugungsmaßnahme wurden alle Bauteile gründlichst mit Perchloräthylen gewaschen, das ohne Erneuerung nur für wenige Waschungen benutzbar war. Nach dem Waschen wurden die Metallteile in Wasserstoff geglüht oder durch HF-Erhitzung entgast. Alle derart behandelten Teile mussten anschließend in geschlossenen Kästen staubsicher zur Montage überführt werden. Die Teile, die noch auf Vorrat genommen wurden, bewahrte man zur größeren Sicherheit in Schutzbehältern auf.
2. Einzelteile
Katode
Die Röhrenausfälle, die auf spezifische Katodeneigenschaften beruhen, konnten schwerer beeinflusst und kontrolliert werden, als elektrische und mechanische Fehler, Mängel wie:
1. Erschöpfung der Emissionsfähigkeit
2. Bildung von Zwischenschichten
3. Zersetzungs- und Verdampfungserscheinungen der Oxidpaste
4. Vergiftungen durch Gasabgabe einzelner Elektroden oder Aufbauteilen.
Die beiden ersten Punkte führten zu einer Verminderung der Verstärkung und die letzteren zu Isolationsfehlern und thermischer Gitteremission.
Die aufgeführten Katodeneigenschaftsmängel wirkten sich umso weniger auf die Lebens-dauer aus, je größer die wirksame Katodenoberfläche bzw. je geringer die spezifische Belastung der Katode ist. Verglichen mit normalen Empfängerröhren, deren Katoden-belastung zwischen 25 und 90mA/cm² liegt, sind diese bei Verstärkerröhren für industrielle und kommerzielle Anlagen mit 10 bis 40mA/cm² niedriger gehalten. Bei der E180F liegt die Katodentemperatur bei Normalheizung im Bereich von 680 bis 690 °C [Schwarztemperatur]. Sie liegt damit etwa um 50°C niedriger als bei älteren Röhrentypen. Die garantierte Lebensdauer von 10000 Stunden erfordert die Einhaltung bestimmter Heizungstoleranzen, deren Abweichung bei Parallelheizung mit ± 5% vom Nennwert der Heizspannung [bei max. Netzspannungsschwankungen von ±10%] und bei Serienheizung mit max. ±1,5% des Heizstromes spezifiziert ist. Eine Röhre verträgt allerdings auch größere Heizspannungsschwankungen, doch können dann vergrößerte Kenndatenänderungen auftreten. Die Überheizung bewirkt vorzeitiges Verdampfen der aktiven Katodenschicht; die Unterheizung führt zur Verarmung der aktiven Katodenoberflächensubstanz. Dennoch ist eine geringe Unterheizung vorteil-hafter, da eine niedrigere Röhrentemperatur die Lebensdauer verbessert, die Katode jedoch dabei nur verringerte Heizspannungsschwankungen verträgt. Die beste Lebensdauer erhält man mit Unterheizung zwischen 3 … 5% bei möglichst hoher Heizungskonstanz von z.B. 1%. Die optimale Heizspannung ist allerdings vom Röhrentyp und von der Katoden-belastung abhängig. Die untere Grenze ist in jedem Fall dadurch gegeben, dass der Sättigungsstrom immer groß gegen den Betriebsstrom bleiben muss.
Alle Katodenhülsen mussten vor und nach dem Besprühen mit Emissionspaste mit Lehren auf Maßhaltigkeit geprüft und die Bedeckung jeder Katode kontrolliert werden, von denen stichprobenweise dann noch einige einer zusätzlich Qualitätsprüfungen mit mikrosko-pischer Oberflächenuntersuchung unterzogen wurden. Auf den richtigen Sitz der Katoden-hülse in den isolierenden Glimmerplättchen war besonders zu achten. Ein Lappen der Katodenhülse, an dem die Katodenzuleitung meist angeschweißt wurde, hatte die Hülse unbeweglich in einem Ausschnitt des unteren Glimmerplättchens fest zu halten. An ihrem unteren Ende erfolgte die Verbindung der Katodenzuleitung mit dem Katodensockelstift aus Sicherheitsgründen mit zweifacher Verschweißung. Damit war sichergestellt, dass in Folge von Ausdehnung oder Schrumpfung durch Ein- und Ausschaltvorgänge keine Unterbrechung in der Katodenzuführung, noch in den Heizleitungen entstehen konnte.
Brenner
Die Heizfäden bestehen üblicherweise aus Wolfram und sind mit Aluminiumoxid bedeckt. Jeder einzelne Heizer wurde auf Unterbrechung der Isolationshülle und auf Güte der abgeflachten Anschlussstellen geprüft. Beim Einsetzen der Fäden in die Katodenhülsen war absolut wichtig, dass die Isolierschicht nicht beschädigt wurde.
Die immer wieder auftretenden Brennerfehler beruhen hauptsächlich auf drei Ursachen:
1. übermäßige Temperatur im inneren des Kerns
2. Beschädigungen der Isolierschicht am Katodenende durch Vibrationsbewegungen des Brenners in der Katode
3. beginnender Bruch des Brennerdrahtes bei scharfen Abbiegungen.
Abhilfe
Durch einen dickeren Kerndraht ließ sich die Arbeitstemperatur erniedrigen. Dies erforderteallerdings eine Drahtverlängerung mit zusätzlichen Windungen, die damit dem Brenner auch einen besseren Sitz in der Katodehülse gaben. Da die Brenner immer scharfe Abknickungen aufweisen und an diesen Stellen bruchgefährdet sind, bedurfte es weiterer Verbesserungen. So wurde der biegsame Kehr-Doppelwendelbrenner eingeführt, wodurch sich ein größerer Drahtdurchmesser verwenden ließ. Die Brennertemperatur konnte damit bis auf einen sicheren Wert herabgesetzt werden, besaß keine scharfen Enden mehr und ließ sich trotz späteren festen Sitzes leicht ohne Beschädigungen in die Katodehülse einschieben. Eine andere Verbesserung erreichte man mit einem Brennerhalter, der im unteren Glimmerteil befestigt unter der Katode vorspringt. In dieses Gebilde ließ sich so der Brenner vor der Montage des Unterteils in den Glasfuß mit sicherem Blick einsetzen und anschweißen. Außerdem ließen sich damit die Fußdrähte an den Brennerhaltern in der Nähe des Glimmerumfangs an-schweißen und gaben so einen guten Halt für den gesamten Röhrenaufbau.
Gitter
Besondere Sorgfalt, Präzision und Sauberkeit erforderte die Fertigung der Gitter. Es ist eines der mechanisch feinsten Systeme der Röhre und dementsprechend empfindlich. Schon zur Prüfung der Gitter kam nur die optische Prüfung infrage, da die üblichen mechanischen Werkzeuge die empfindlichen DrähteA hätten beschädigen können. Die Prüfung erfolgte u.a. mit einem
Projektionsgerät bei 25-facher Vergrößerung. Anders wären die Fertigungstoleranzen kaum kontrollierbar gewesen, zumal die Abstände der Löcher in den Glimmerisolatoren oft nur 6-8µm betrugen und die Toleranz der Gitterstege wie z.B. bei der E180F mit ±3 µm einzuhalten waren.
Das hohe S/C-Verhältnis, das für Breitbandverstärkerröhre gefordert war, konnte u.a. durch kleine Gitter-Katodenabstände und dünne Gitterdrähte erreicht werden. Legte man Wert auf kleine Röhrenabmessungen und geringe Heizleistung, so stieß man mit Rücksicht auf die mechanische Stabilität der Systeme bei normaler Gitterbauweise an die Grenze des machbaren.
Dazu zwei typische Röhrenbeispiele:
1. Typ 18042 G/k -Abstand = 120 µm; Gitterdraht D= 40,0 µm
2. Typ E180F " = 53 µm; " D= 7,5 µm
Die Werte des ersten Beispiels ließen sich noch mit konventioneller Gitterkonstruktion beherrschen. Beim zweiten Beispiel konnten sich die Gitter nicht mehr selbst tragen und mussten deswegen als sog. Spanngitter ausgeführt werden. Dazu wurde der Gitterdraht aus Wolfram mit hoher Vorspannung auf einen steifen Rahmen, bestehend aus zwei gezogenen Molybdänstäben mit vier aufgeschweißten Molybdänbändern, gewickelt. Die hohe mechanische Vorspannung der Gitterdrähte stabilisierte die Konstruktion insgesamt.
Dem Auftreten von Gitterströmen galten alle erdenklichen Vorsichtsmaßnahmen, haupt-sächlich verursacht durch:
1. Gitteremission
2. schlechte Isolation
3. schlechtes Vakuum.
Die beiden ersten Fehlerquellen ließen sich konstruktiv bzw. durch entsprechende Ferti-gungsvorkehrungen vermeiden; schlechtes Vakuum durch verschiedene bereits erwähnte Maßnahmen.
A Die Drähte als wichtige und empfindliche Komponente für Brenner und Gitter werden bei
Liefereingang von einer Materialprüfstelle auf Dehnung und Zerreißfestigkeit geprüft.
Verfahren gegen Gitteremission
Eine wirksame Möglichkeit Gitteremission entgegen zu wirken, bestand in einer guten Ableitung der Wärme von den Gittern [vornehmlich g2 und g1].Entweder durch kupferne Gitter-stäbe bzw. zusätzlich zur Aufnahme bzw. Abstrahlung an ihren Enden angeschweißten Kühlfahnen[Wärmekonvektion]. So konnte die Gittertemperatur im Allgemeinen in unkritischen Bereichen gehalten werden. Auch vergoldete Gitterdrähte kamen zur Anwendung [Steuergitter bei steilen Röhren], da Gold eine hohe Elektronenaustrittsarbeit besitzt; z.B. bei Röhren wie CCa, E55L, E81L, E180F, E810F, E288CC und anderen Spezialröhren. Die Fertigung der Rahmen- und deren Gittervergoldung erfolgte in getrennten Arbeitsgängen; die Vergoldung der Rahmen durch Oxidation und Reduktion elektrolytisch erst nach vorheriger Aufrauung der Oberfläche. Im Gegensatz dazu wurde der Gitterdraht feuer-vergoldet, indem der Draht durch einen im HF-Feld erhitzten Goldtropfen gezogen wurde. Zur Befestigung dieses Drahtes auf dem Steg benutzte man einen Glasüberzug auf der Außenseite des Steges. Mit Rücksicht auf das Kontaktpotenzial wurde die Vergoldung meist nur in Ausnahmefällen eingesetzt.
Maßnahmen gegen Gitterströme
1.sorgfältige Glimmerauswahl
2.Vergrößerung der Kriechwege auf den Glimmerisolatoren durch Besprühen mit Magnesiumoxid.
3.Verlängerung der Isolationsstrecken zwischen den Anschlussstiften der Röhrensockel.
Die Ausbildung des Röhrenfußes als Pressteller war ein deutlicher Fortschritt im Röhrenbau. Bei kritischen Röhren ließen sich die Isolationsstrecken so durch vergrößern der Glaskegel- Stiftdurchführungen künstlich verlängern, wobei gleichzeitig mehr Sicherheit gegen Undichtigkeiten bzw. Luftzieher entstand. Bei einigen Röhrentypen setzte man z.B. im Bereich Sockel-Systemunterkante zusätzlich Glimmerscheiben ein, die einen Teil des Presstellers abdeckten, um einen Niederschlagen von Barium oder Magnesium zwischen den Gitteranschlüssen und den übrigen Durchführungen zu verhindern. Beide Maßnahmen trugen beträchtlich zur Verringerung von Gitterströmen und Störgeräuschen bei.
IV. Aufbau
Der Zusammenbau der diversen Einzelteile erfolgte in verschiedenen getrennten Arbeits-gängen, ein Fehlerquellenpotenzial, was zusätzliche Überwachungen der Systemmontage mit ständiger Kontrolle auf Korrektheit und Sauberkeit unerlässlich machte.
Die komplette Montage hatte in Sauberräumen mit künstlicher, staubfreier Belüftung zuerfolgen. Hierzu dienten Windfänge, Klimatisierung und ähnliches bei ständiger Über-wachung des Luftstaubgehaltes. Die Räume selbst mussten mit einem geeigneten Fußboden-belag sowie Wand- und Deckenanstrich versehen sein, um Fusselbildung weitestgehend zu vermeiden. Und für die Montiererinnen war eine bestimmte Kleidung nach den gleichen Gesichtspunkten festgelegt; das Rauchen in diesen Räumen strengstens untersagt.
Die Röhreneinzelteile und Systeme waren grundsätzlich in staubfreien Behältern auf-zubewahren. Die fertigen Systeme mussten möglichst unmittelbar nach Fertigstellung in den Kolben eingesetzt werden, damit sie bis zum Einschmelzen keinen Schaden mehr durch Staub nehmen konnten.
Um die Röhren während der Montage vor Verunreinigungen zu schützen, arbeitete man zweckmäßigerweise so, dass der Montageraum komplett unter einem geringen Überdruck gesetzt wurde und die Montageplätze mit einer zusätzlichen Plexiglashauben geschützt wurden, oder man verwendete Arbeitstische mit aufgesetzten Überdruckkabinen, in denen die Montage des Elektrodenaufbaus erfolgte. Vermehrt auftretende Röhrenausfälle durch Kracheln oder entstandene Isolierfehler durch verkohlte Fusseln, waren fast immer durch mangelhafte Sauberkeit oder Vorschriftenmissachtung des Montagepersonals verursacht, d.h. ihre Qualifikation und Sorgfalt hatte entscheidenden Einfluss auf die Produktqualität und Höhe der Fertigungsausbeute.
Häufige Montagefehler entstanden durch zu viele und schlechte Schweißstellen, obwohl nur unter Einsatz von Montagelehren geschweißt wurde. Mit Reduzierung der Anzahl der Schweißstellen und mit Schulungsmaßnahmen des Personals ließ sich diese Problematik allgemein schnell lösen.
Die Forderung nach Reduzierung der Anzahl von Schweißstellen war häufig relativ einfach durch konstruktive Änderung machbar, doch an die 20 Schweißpunkte je Röhre verblieben im allgemein dennoch. Das Erreichen zuverlässiger und reproduzierbarer Schweißungen verlangte hohe Präzisionsaufwendung, aber auch konzentrierte Arbeitsausführung, zumal die Einstellung des Schweißwiderstandes der Geschicklichkeit der betreffenden Arbeits-kraft einschließlich nachfolgender Kontrolle überlassen war. Deutliche Verbesserungen und Kontinuität der Schweißungen brachten später neuere sensitivere Schweißgerätegenerationen mit Begrenzereinrichtung, mit denen reproduzierbare Schweißungen sicherer wurden.
Trotz dieser Optimierung bestand weiter Anlass den Systemaufbau und deren Montage bereits zwischen den einzelnen Fertigungsgängen anhand spezieller Kontrollen wie z.B. Schliffuntersuchungen oder auch optischer Prüfungen mit Lupe oder mit binokularem Mikroskop zu überwachen. Arbeiten, die meist einer der Fertigung angegliederten Versuchs-abteilung oblagen.
Vor Weiterleitung in Fertigungsabläufe gemäß V., war jedes Stück auf nachstehende Punkte hin zu kontrollieren:
a) richtiger Sitz des Systems,
b) Maßhaltigkeit,
c) Haltbarkeit der Schweißstellen, ohne zu verbiegen,
d) Staubeinschlüsse,
e) mechanische Fehler.
V. Schmelzen und Pumpen
Beide Arbeitsgänge lassen sich nicht streng von einander trennen, da sie kontinuierlich ineinander übergehen. Dabei auftretende Probleme sind vor allem auftretende Glas-Spannungen beim Schmelzen und beim Vakuumpumpen / Evakuieren.
1. Schmelzen
Der Einschmelzvorgang sollte nach Möglichkeit sofort im Anschluss an die Montage erfolgen. Dazu gehört, dass die fertigen Systeme sofort in die Glaskolben eingesetzt werden, um nachträgliche Verunreinigungen durch Staub oder ähnliches zu vermeiden. Der Einschmelzvorgang selbst und die spätere Abkühlung bargen zahlreiche Fehler-quellen in sich. Am meisten handelte es sich hierbei um Glasfehler, deren am häufigsten auftretenden Ursachen und Verhinderungsmaßnahmen sich wie nachfolgend darstellen:
a ) thermische Spannungen
Wie bereits der Name sagt, sind diese auftretenden Spannungen temperaturabhängig. So können sie beispielsweise beim Verschmelzen schlecht zueinander passender Glassorten oder auch bei ungleichmäßiger Abkühlung aus der Schmelze entstehen.
Den auftretenden Spannungen sind zwei Hauptursachen zuzuordnen:
1. verschiedene Ausdehnungskoeffizienten der verwendeten Gläser,
2. unterschiedliche Ausdehnung an Schmelzstellen zu einer entfernteren Stelle.
Hier galt es unbedingt Spannungsringe zu verringern, gar zu vermeiden, die bei zu heißer Verschmelzung von Gläsern entstehen und durch einen zu starken Temperaturgradienten sich schädlich auswirken. Die Spannungsverteilung in einem Spannungsring ist sehr kompliziert. Man kann sie als eine Zone hoher Spannung betrachten, die mit einer dünnen Glasschicht bedeckt ist. Im Laufe der Lebensdauer wird die Röhre[Kolben oder Fuß]durch weitere Spannungskräfte beansprucht, was zur Überschreitung der Zugfestigkeit des Glases führen kann. Eine Kontrolle erfolgt im Spannungsprüfer anhand vergleichender Beobachtung zu bekannten Standard-werten.[optische Veränderungen durch Polarisationsmikroskop oder Verfärbung im Glasspannungsprüfer]Auch ein Riss bietet eine Kontrollmöglichkeit. Er wird mit einem Diamanten vorge-nommen, was bei großen Spannungen zum sofortigen Glasbruch führt.
b) Risse
Als "Riss" bezeichnet man die Stelle, an der ein Glas in seiner Vereinigungsstelle spitze Winkel zwischen ihren Oberflächen bildet. Ein Fachmann kann die inneren Rissedurch Beobachtung der äußeren Umrisse erkennen. Risse in der Verschmelzung des Fußes in den Kolben sind nachweisbar, indem die kalte Röhre in kochendes Wasser getaucht wird, denn jeder Bruchfehler geht von der inneren Oberfläche aus.
c) Undichtigkeiten
Undichtigkeiten treten infolge fehlerhafter Glas-Metall- oder Metall-Keramik Ver-schmelzungen auf. Sie sind abhängig von den chemischen Reaktionen während des Einschmelzvorganges zwischen einer direkt auf dem Metall haftenden Oxidschicht und dem geschmolzenen Glas. Die verschiedenen Reaktionsstufen sind von Farbänderungen begleitet. Die visuelle Beobachtung der Einschmelzfarbe ist daher ein probates Prüfverfahren zur Vakuumdichtigkeit. Außerdem kann die Röhre in eine viskose fluoreszierende Flüssigkeit eingetaucht werden, wobei diese in die Undichtigkeit eindiffundiert und bei zusätzlicher Bestrahlung mit ultraviolettem Licht sichtbar wird. Feine Undichtigkeiten lassen sich dagegen nur durch Lagerung und charakteristische Zerstörung nachweisen. Dabei wirkt eine Lagerung in Wasserstoff bei einem Druck von 7 kg/cm² beschleunigend.
Nachdem die Einschmelzdrähte schon in der unter "Material" beschriebenen Weise untersucht worden waren, kamen unter Einbeziehung des Ausdehnungskoeffizienten noch ergänzende Verschmelzversuche dazu.
Nach dem Einschmelzen mussten die Röhrenkolben gleichmäßig abkühlen, indem sie einen Temperofen mit drei Temperaturbereichen zu durchlaufen hatten. Zum Schutz der Systeme gegen Oxidation wurden die Röhrenkolben dabei ebenso wie vorher auf der Einschmelzmaschine ständig mit frischem Schutzgas gefüllt.
Zur Prüfung auf schädliche Spannungen stellte man beim täglichen Anlauf der Fertigung auf den Einschmelzmaschinen eine Anzahl Blindröhren her und schnitt sie dann zwecks genauer Untersuchung wieder auf. Außerdem wurden stündlich aus der normalen Fertigung Röhrenproben entnommen und auf die gleiche Weise untersucht.
2. Pumpen
Dem Auspumpen galt höchste Sorgfalt. So wurde eine Langlebensdauerröhre durch-schnittlich vier bis sechsmal länger evakuiert als eine normale Rundfunkröhre. Ent-sprechend aufwendig wurden auch die Metalle vorentgast, die Glasausheizung auf der Pumpe sowie die Entgasung der Systeme mit größerem Zeitaufwand und erhöhter Sorgfalt durchgeführt. Für das Getter verwendete man besonders hochwertige Materialien bzw. verdampfte sogar zwei hochaktive Getterpillen. Um den Niederschlag des Getters am oberen Kolbenteil (Dom) zu lenken, leitete man beim Gettern eine kühlende Luft-strömung über den Kolbendom.
Das Abschmelzen der Röhre mit Abziehen des Pumpstängels erwies sich als häufigste Fehlerquelle, was eine generelle Güteuntersuchungskontrolle des abgeschmolzenen Pump-stängels erforderte.
Außerdem wurden stichprobenweise Röhren eine Minute lang in kochendes Wasser getaucht. Exemplare mit kritischer Spannung wurden dabei zerstört. Durch andere schon beim Einschmelzen am Pumpautomaten stichprobenweise entnommene geprüfte Röhren, ließ sich, bevor die ersten fertig formierten Röhren zum Prüffeld gingen, feststellen, ob die Einschmelzung und das Pumpen richtig verlaufen wird bzw. ob Korrekturen vor-zunehmen wären. Betrug der Ausfall der Probenreihe mehr als 5%, wurde das komplette Fertigungslos abgelehnt.
VI. Prüfungen
Bei den an den Röhren vorgenommenen Messungen und Untersuchungen klassifizierte man in zwei Gruppen:
Prüfung der Gruppe A:
Hierunter standen Prüfungen, die an allen Röhren vorzunehmen waren (vergleichbar mit statischem Prüffeld).
Prüfungen der Gruppe B:
Hierunter liefen Prüfungen aus Stichprobenentnahmen, die der Qualitätskontrolle dienten. Bei einem Verwurf der Probereihe um mehr als 5% bedeutete dies Ablehnung des ganzen Fertigungsloses.
1. Prüfungen der Gruppe A:
Diese Prüfungen begannen mit der subjektiven Betrachtung des gefertigten Aufbaus und der Kontrolle nach dem Schmelzen und Vakuumspumpen. Danach durchliefen alle Röhren den Aktivierungsprozess. Hierbei wurden etwa 250 Volt zwischen jede Elektrode -bezogen auf alle übrigen geerdeten Elektroden- gelegt und damit Fussel beseitigt bzw. Kurzschlüsse nachgewiesen. Um mögliche Brennerfehler auszusortieren, wurde kurzzeitig [etwa 10 Sek. lang] eine hohe Spannung an den Brenner jeder Röhre gelegt. Dann folgte die Messung der Röhre auf ihre elektrischen Kennwerte, mit an-schließender Kurzschluss- und Schüttelprüfung von mindestens eine Minute bei 50Hz und einer Amplitude von 0,5mm. Dabei wurden die Röhren unter A-Klasse Verstärker-bedingungen betrieben und gleichzeitig die Störspannung am Ausgang des Anoden-kreises gemessen. Im weiteren Verlauf erfolgte für alle Röhren ein 10-stündiger Test unter A-Verstärker Betriebsbedingungen. Im Weiteren folgte bei Unterheizung eine Prüfung der Katodenaktivierung mit anschließender Wiederholung der elektrischen Prüfung. Für eine Probenmenge von 12 Röhren wurden vor- und nach einem zehn-stündigen Prüfbetrieb Messkurven aufgezeichnet, die nach Abschluss miteinander verglichen wurden. Aus dem Vergleich der Ergebnisse ließ sich erkennen, ob bzw. welche Veränderungen die Röhren erfahren hatten.
Selbstverständlich wurden je nach Art der Röhre auch deren Funktionswerte wie Steilheit, Verstärkung, Leistung, Geräuschfreiheit und andere Parameter stets zu 100% gemessen.
Um einen stabilen Anhaltspunkt zu erhalten und gleichzeitig eine eventuell zu Beginn der Lebensdauer vorhandene Abweichung der Lebensdauerkurve vom angestrebten Verlauf auszugleichen, wurden alle Röhren unter normalen Betriebsbedingungen 50 Stunden lang gealtert.
Die Endprüfung der Röhren begann damit, dass sie in einer A-Verstärkerschaltung im Dauerbetrieb auf einem Rütteltisch Beschleunigung von 2,5g* oder kurzzeitig bis 5g unterworfen wurden. Diese Prüfung deckte alle losen Kontakte oder Geräusch-störungen auf, vorwiegend durch Staubeinschlüsse hervorgerufen. Fielen hierbei zu viele Röhren aus, bestand dringliche Veranlassung steuernd in die Fertigung ein-zugreifen. Außerdem wurden die Röhren noch einer Stoßprüfung unterzogen, die ebenfalls unter angelegter Spannung erfolgte. Dabei machte die Röhre die Bewegung eines Hammers mit, der jede Sekunde mehrfach angehoben und wieder fallen gelassen wurde. *Erdbeschleunigung g=9,81 ms-2
Bei einem anderen Testverfahren wurde die Röhre dagegen auf einem beweglichen Tisch befestigt, der von einem Hammer angestoßen wurde. Die Prüfung erfolgte mit je 5 Stößen in verschiedenen Richtungen, wobei Beschleunigungen von 500g während einer ms auftreten. Die Störspannung, die dabei am Anodenwiderstand ermessen wurde, gab Aufschluss über die Stabilität des Systemaufbaus -siehe unter II. konstruktive Maßnahmen.
Nach der Endprüfung gingen die fertigen Röhren zunächst für einen Monat ins Lager. Erst dann erfolgte die endgültige Vermessung mit Prüfung des Vakuums. Waren die Prüfungen einer zweiten "B-Gruppe" auch erfolgreich, konnten die Röhren ausge-liefert werden. Zur Überwachung der Röhrenwerte auf Mittelwert und Streuung der Einzelwerte gab es auch ein ökonomischeres Verfahren. Schon aus 20 Messwerten wurde der Fertigungsmittelwert mit einer Genauigkeit von ± 22% der Streubreite des fraglichen Kennwertes ermittelt, wenn der Kennwert selbst um z.B. ± 15% seines Soll-wertes schwankte. Daraus ergab sich z.B. als mutmaßlicher Mittelwertsfehler ein Wert von ±3,3%, d.h. entsprechend±22% von 15%. Dieses Verfahren in Anwendung bot eine gleichwertige aber schnellere und dynamischere Möglichkeit um korrigierend in eine laufende Fertigung einzugreifen.
2. Prüfungen der Gruppe B:
Allgemein:
Hierunter liefen Prüfungen der Qualitätskontrolle, mit zu verschiedenen Zeiten der Herstellung aus der Serie entnommen Prüflingen. Damit verfolgte man den Zweck, sicherzustellen, dass die Originalqualität erhalten blieb. Hierzu gehörten bereits die Kontrollen auf Vorhandensein von Spannungsringen nach dem Pumpen und Schmelzen. Die Genauigkeit, die in einer Stichprobenprüfung erreichbar war, hing von der Größe der Stichprobe und vom Anteil der Ausfallröhren in der Gesamtheit ab. Wenn z.B. anhand einer Stichprobe von 75 Stück sichergestellt werden sollte, dass der Ausschuss in der Lieferung mit 90% Sicherheit nicht mehr als 3% betrage durfte, so lautete die Forderung, "Stichprobe ohne Ausfallröhren". Diese Forderung war so scharf, dass noch Lose mit nur 0,2% Ausschussröhren in einem von 10 Fällen -fälschlicherweise-als schlecht zurückgewiesen werden mussten. Erhöhte man die Stichprobe auf 300 Stück, so durften 4 Ausfallröhren in ihr enthalten sein und die Lose, die in einem von 10 Fällen fälschlicherweise zurückgewiesen wurden, enthielt mindestens 0,8% Ausschuss. Die Zahl der unnötigen hundertprozentigen Messungen würde also soweit abnehmen, dass es sich lohnte, die Stichproben etwas größer zu machen. Derartige Stichproben lagen daher auch meist zwischen Entnahmenmengen von 75 und 300 Stück.
Nachstehend Details zu den einzelnen Messungen:
a) Resonanzprüfung:
Hierbei sitzt die Röhre auf einem Halter, der mit einer Spule verbunden ist, die mit einer Vibrationsfrequenz von 15-3000 Hz variabel betrieben wird. Unter einer Beschleunigung von 2,5g wird der ausgehende Wechselstrom der Röhre parallel zum Außenwiderstand beobachtet. Dies erfolgte mit Hilfe eines Resonanzkurven-schreibers oder eines Röhrenvoltmeters und Oszillografen. Mit dem Alternativ des Resonanzverfahrens ließ sich die Vibrationskomponente mit einem Mikroskop und einer stroboskopischen Lampe ermitteln. Die Ergebnisse wurden aufgezeichnet und in ihrer Größe mit einer Vorgabe verglichen, die die Entw.-Abtlg. erarbeitet hatte.
b) Ermüdungsprüfungen:
Diese Prüfung geschah auf im Prinzip gleicher Apparatur wie unter a) aufgeführt. Die Röhren wurden in den drei hauptsächlichen Lagen etwa 90 Stunden geschüttelt, wobei die Schüttelfrequenz und die Beschleunigungsamplitude zwischen 2 und 3g variiert wurden. Unter den Betriebsbedingungen eines A-Verstärkers erfolgte dabei ebenso eine Messung im Anodenkreis, wobei man den Brenner zusätzlich im 5 Minutenzyklus ein- und ausschaltete. Löste sich eine Elektrode, so erkannte man diese Fehlerquelle an auftretenden geräuschverursachenden Anodenstrom-schwankungen, die zu einem späterem Kurzschluss oder einer Unterbrechung führen würden. Die Geräuschprüfung gab so frühzeitig Hinweis auf derartig unan-genehme Fehlerquellen.
c) Stoßprüfung:
Für die Stoßprüfung wurde ein Prüfling fest auf eine Plattform montiert und diese durch einen Fallhammer angestoßen. Die Stärke des Stoßes lag in der Größenordnung von 1000g. Die kalte Röhre erhielt fünf Schläge in jeder der drei Ebenen, d. h.
1. in horizontaler Ebene mit der langen Achse senkrecht zu der Ebene der
Erschütterung,
2. in der horizontalen mit der langen Röhrenachse parallel zu der Ebene der
Erschütterung,
3. vertikal.
Im Fall der vertikalen Lage wurde der Schlag auf beide Röhrenenden gegeben und während der Stöße auftretende Kurzschlüsse gezählt.
Nach Abschluss der unter a, b, und c aufgeführten Prüfungen wurden alle Röhren einer nochmaligen elektrischen Vermessung unterzogen.
VII. Lebensdauer:
Die Lebensdauerprüfungen bei modernen Röhren nahmen über deren zeitlichen Entwicklung mit zunehmend an sie gestellt gestiegenen Anforderungen stetig zu. Im Lebensdauertest mussten die Röhren aus diesem Grunde in großer Zahl über längere Zeit unter den Grenzbedingungen des Datenblattes betrieben und währenddessen in gestaffelten Zeitabschnittvermessen werden. Veränderungen in der Röhrencharakteristik während der Lebensdauerprüfung waren oft auf Kontaktpotenzialänderung zurückzuführen. Besonders zu Beginn der Lebensdauer bewirkten die komplizierten physikalischen und chemischen Prozesse in der Röhre eine Verschiebung des Kontaktpotenzials und damit des Arbeits-punktes. Um einen stabilen Arbeitspunkt zu erhalten, wurden deswegen alle Röhren 50 Stunden lang unter normalen Betriebsbedingungen gealtert. Mit dem Alterungsprozess erhielt man gleichzeitig Aussagen über deren Qualität. Die bereits beschriebenen Maßnahmen zur Unterdrückung des Gitterstromes offenbarten hierbei ihre eminente Wichtigkeit.
Die für die Stichprobenmessungen entnommenen Röhren wurden außerdem ca. 500 Std. unter verschärfte elektrische Bedingungen oder über 2000 Stunden unter normale statische Lebensdauerprüfbedingungen gesetzt. Durch die erhöhte elektrische Beanspruchung traten dabei Fehler früher in Erscheinung als bei normaler Belastung. Die dabei entstandenen Ausfälle ermöglichten eindeutige Rückschlüsse auf das Verhalten der Röhre für die spezifizierte und propagierte Lebensdauer [-Kurve], in die ergänzend Zusammenhänge aus den Vibrationsuntersuchungen einflossen, die gewöhnlich erst 2 Wochen nach dem Lebensdauerlauf folgten, mit Ergebnisvervollständigung des Verhaltens während der ersten Lebensdauerstunden der Probe. Das Ergebnis dieser Lebensdauerprüfung entschied darüber, ob das Fertigungslos ausgeliefert werden konnte oder nicht. Die Zuverlässigkeit eines Röhrentyps wird allgemein durch den Röhrenausfall in‰ je 1000 Stunden, dem sog.
"P-Faktor", gekennzeichnet. Hierzu wird in einem Diagramm als Kurve zeitlich der Prozent-anteil der noch in Betrieb befindlichen Röhren dargestellt. Der Maßstab für p= Prozentsatz ist logarithmisch, der für die Zeit= t linear. Das Ende der Lebensdauer einer einzelnen Röhre, im Sinne der Lebensdauergarantie, ist durch das Unterschreiten von Grenzdaten definiert und für jeden Typ unterschiedlich festgelegt. So bewegen sich die definierten Grenzwerte für Anodenstrom und Steilheit am Ende der Lebensdauer bei etwa 70% des Nennwertes.
In der Lebensdauergarantie eingeschlossen ist, dass diese Grenzwerte bei Einhalten der Nenn-belastung erst nach Ablauf der garantierten Lebensdauer unterschritten werden dürfen. Selbst-verständlich können die Röhren auch bei niedrigeren Kennwerten weiter betrieben werden. Da die Angabe verbindlicher Lebensdauerwerte mit gewissen Schwierigkeiten verbunden ist, die schon dadurch gegeben sind, dass großen Stückzahlen über sehr lange Zeit zu kontrollieren wären[10000 Stunden ca. 14 Monate], hat man sich auf Angaben bei Nennlast zu beschränken.
Anwendung in der Praxis und Rückschlüsse
Aus allen vorgenannten Ausführungen geht hervor, dass es sich bei Langlebensdauerröhren nicht um Röhren handelt, die durch besonders scharfe Prüfung aus Fertigungspartien selektiert werden, sondern das Ergebnis gründlicher Entwicklung, sowie einer bis ins letzte durchdachten und erprobten Fertigungstechnik und Prüfungen sind. Das Bemühen einer steten Erhöhung der Zuverlässigkeit von Röhren ist immer ein Kampf um Bruchteile eines Prozent Ausfall gewesen und bedurfte deswegen zur Sicherstellung unterschiedlichster Erprobungs- und Testmaß-nahmen. Daher war es geboten, die Röhren im Betrieb weiter zu verfolgen und insbesonders ausgefallene Röhren auf dessen Ursache zu untersuchen. Die reklamierten Röhren wurden ge-sammelt und geprüft, wobei meist vorweg schon Kundenangaben wertvolle Hinweise auf die dann selbst ermittelte Ausfallursachen gaben. Zur laufenden Überwachung wurde für jeden Röhrentyp eine Ausfallstatistik als Tendenzdokument für Verbesserung- bzw. Verschlech-terung geführt und letztendlich mit den Lieferzahlen in Beziehung gesetzt. Die damit gewonnene grafische Auswertung lieferte ein getreues und täglich sich schärfendes Bild des erreichten Fertigungs-, Quantitäts- und Qualitätsstandes. Als erweiterte Maßnahme mussten Röhren auch in praktisch betriebener Anwendung überwacht werden, oft auf Veranlassung spezieller Kunden-Schaltungsanwendungs-Problematiken, zumal die europäische Technik des Gerätebaus, im Gegensatz zur amerikanischen stets mit möglichst wenig Röhren auszukommen trachtete, manchmal mit Schaltungen arbeitete, die auf Nebeneigenschaften von Röhren aufgebaut waren, deren Einhaltung in der Serie nicht ohne weiteres zu gewährleisten waren.
Negativen Einfluss auf die Zuverlässigkeit von Röhren mit Glasfüßen entstand zu Beginn der Presstellertechnologie durch Unverträglichkeit Röhre/Fassung, die den Röhrenhersteller zu einer Lösungsfindung herausforderte und zu der Auflage führte, Röhren vor Einsetzen in eine Fassung mit einer Stiftlehre zu richten.
Analysen belegen, dass ungenügend ausgebildetes Personal durch fehlerhaftes Einsetzen der Röhre Ausfallquoten von 3% oder mehr produzierten.
*Der Ausdehnungskoeffizient wird in einem Dilatometer gemessen. In einem elektrisch beheizten Ofen befindet sich die Messprobe zwischen 2 Quarzhalterungen, von denen die untere feststeht, während die obere leicht beweglich gelagert ist. Die obere endet in einer Kondensatorplatte, der eine zweite Platte parallel gegenüber steht. Durch Ausdehnung der Messprobe ändert sich die Kapazität des Kondensators, und diese Änderung ist ein Maß für die Längenänderung derProbe und kann mit einer Präzisions-Kapazitätsmessbrücke gemessen werden. Soll der absolute Ausdehnungskoeffizient ermittelt werden, dann muss von dem gemessenen Wert die Apparatekonstante abgezogen werden.
Wolfgang Scharschmidt >für radiomuseum.org< Auszug aus Röhrenhistorie Band I ©
Für diesen Post bedanken, weil hilfreich und/oder fachlich fundiert.