elac: RD100; Kunststoffgehäuse Restauration
12
ID: 195665
Dieser Artikel betrifft das Modell: RD100 (Elac Electroacustic GmbH; Kiel)
elac: RD100; Kunststoffgehäuse Restauration
26.Jul.09 00:42
3966
12
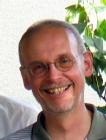
Im RM.org gibt es zur äußerlichen Restauration von Kunststoffen hier etliche Hinweise.
In den 50er-70er Jahren wurde bei Radios häufig Polystyrol (PS) und später High Impact Polystyrol (HIPS) verwendet. PS wurde seit 1937 von den IG Farben produziert. Als Radiogehäuse wurde es erst in den 50 Jahren in Deutschland verbreitet eingesetzt. Polystyrol allein ist ziemlich bruchempfindlich, daher wurde HIPS entwickelt, hier ist dem Polystrol als zweite Phase feinverteiltes Gummi beigemischt, wodurch das PS wesentlich bruch- und schlagfester wird, eben HIPS. Heute sind Gehäuse neben HIPS (z.B. Fernseher, Kühlschränke) auch häufig aus Acrylnitril-Butadien-Styrol (ABS, seit 1948 großtechnisch produziert) (z.B. Handys, Kaffemaschinen, Autoteile) hergestellt, das noch bessere Bruch- und Schlageigenschaften hat.
PS, HIPS und Abs sind sogenannte Thermoplaste, d.h. sie können durch erwärmen immer wieder erweicht werden. Sie werden typischerweise im Spritzgußverfahren hergestellt. Unter hohem Druck wird die erweichte zähflüssige Kunststoffmasse in Stahlformen gepresst. Das lohnt sich nur bei hohen Stückzahlen, da die Herstellung der Stahlformen sehr teuer ist.
Im Gegensatz hierzu können Duroplaste durch Erwärmen nicht wieder verflüssigt werden. Unter Radiosammlern ist Bakelit der älteste und bekannteste Duroplast. Es handelt sich um ein Polymer aus Phenol und Formaldehyd. In USA wurden Ende der 30er Jahre Radiogehäuse aus „Catalin“ hergestellt, einem dem Bakelit ähnlichen Duroplast, der im Gegensatz zum Bakelit von Natur aus nahezu farblos ist und daher gut mit Farbpigmenten eingefärbt werden kann. Diese bunten, kleinen „Catalinradios“ sind heute begehrte Sammlerstücke in USA. Sie konnten in billigen Aluminiumformen gegossen werden. Obwohl sie technisch sehr einfach sind und als Zweitradio für die Küche oder Schlafzimmer gedacht waren, wurden für seltene Farbvarianten dieser Art Deco Radios mehrere tausend US$ von Sammlern bezahlt. Siehe hier . Catalin ist nicht so dauerhaft wie Bakelit und verwittert an der Oberfläche. Daher werden diese Radios oft ähnlich wie im folgenden beschrieben restauriert.
Zurück zum RD100 von ELAC. Das Gerät ist aus PS oder HIPS hergestellt. In Gehäusen findet man heutzutage Angaben zum Kunststoff um das Recycling zu erleichtern. Das war in den 50-70er Jahren nicht immer üblich. Dafür gab es oft Presszeichen
Mein Gerät fand ich auf einem Flohmarkt. Die Klappziffern machen das Gerät in heutigen Augen zum Exoten, aber in jener Zeit war es eine der wenigen Möglichkeiten eine deutliche und ruhige Digitalanzeige von akzeptabler Größe zu realisieren. (Innenaufnahmen siehe unter dem Model)
Es war ziemlich verdreckt und hatte offensichtlich in einer Werkstatt gestanden, da auf dem Gehäuse deutliche Lötkolbenspuren zu sehen waren (Bild 1). Der Preis von 3,- € machte es zu einem hervorragenden Übungsobjekt für die Restauration eines modernen Gehäuses.
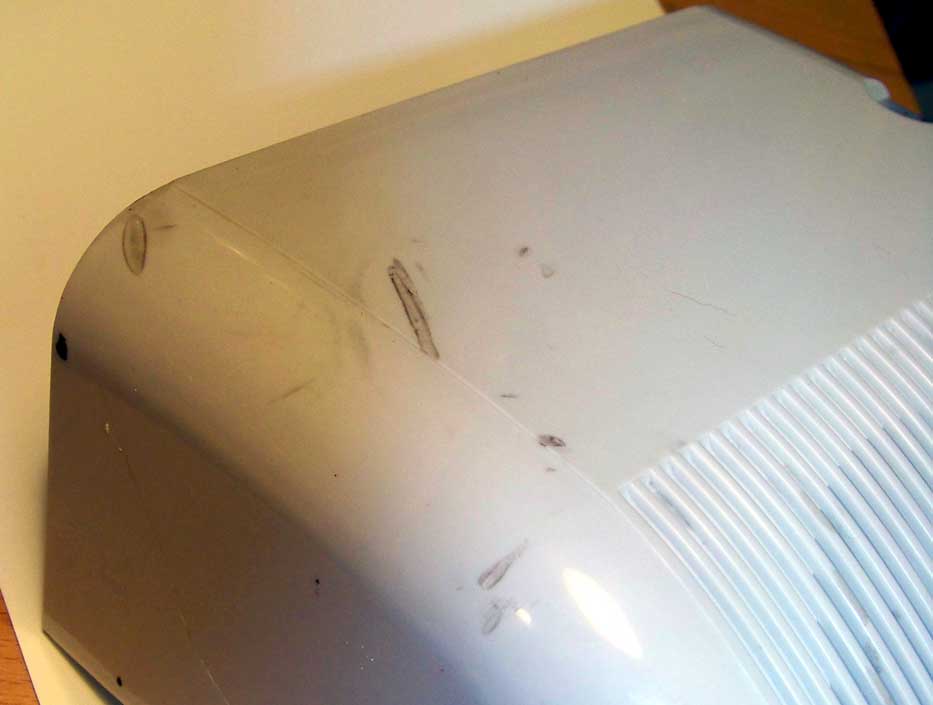
Eine erste Überprüfung zeigte, dass das Gerät elektronisch vollkommen intakt war. Das Radioteil und der Klang sind von erstaunlicher Qualität und die Ziffernanzeige funktionierte tadellos. Also ran an die Lötkolbenspuren.
Das Gehäuse wurde abgeschliffen beginnend mit 80er Schleifpapier, 320, 400, 600 und 1200. Alternativ zu 1200er tut es auch Stahlwolle 000. Die Erfahrung zeigte, dass 80er Papier zwar schnell die Furchen des Lötkolbens zum Verschwinden brachte, aber auch neue Kratzer im Gehäuse erzeugte, die später mit feinerem Papier nur schwer zu entfernen waren. Ich empfehle daher mit 180er Papier zu beginnen.
Das Schleifen fand immer per Hand und unter Wasserzugabe statt. Es ist zu bedenken, dass wir hier, wie oben erläutert, einen Thermoplasten vor uns haben, der bei zu großer Hitzeentwicklung durch den Schleifprozess erweichen würde, was die Oberfläche zerstören würde.
Nach dem letzten Schliff mit 1200er Schleifpapier oder Stahlwolle 000 (funktioniert bei den Rundungen besser) wurde auf Schleifpaste gewechselt. Auch hier wurde ausschließlich per Hand poliert. Das geht relativ schnell und gut. Zuerst habe ich eine Chrompolitur verwendet. Es stellte sich aber heraus, dass diese immer noch zu grob war. Die Oberfläche hatte noch keinen zufriedenstellenden dem Original entsprechenden Glanz.
Den letzten Schliff bekam das Gerät mit „Universal Polishing Paste“ der Firma Ivoclar Vivadent AG, die von Zahnärzten zum Polieren von Zahnprothesen verwendet wird. Man erhält sie in Universitätsstädten in Geschäften, die die Zahnmedizinstudenten mit Materialien versorgen. Es ist eine rosa Paste, offensichtlich mit den für Polierpasten üblichen Zusätzen von Petroleum, Ammoniak und Wachs.
Bild 2 und 3 zeigen das Ergebnis der Bemühungen. Ich war erstaunt, wie leicht sich das Gehäuse wieder in den Originalzustand versetzen ließ, trotz der Lötkolbenspuren. Auch die Sichtscheibe ließ sich mit o.g. Polierpaste von Kratzern befreien.
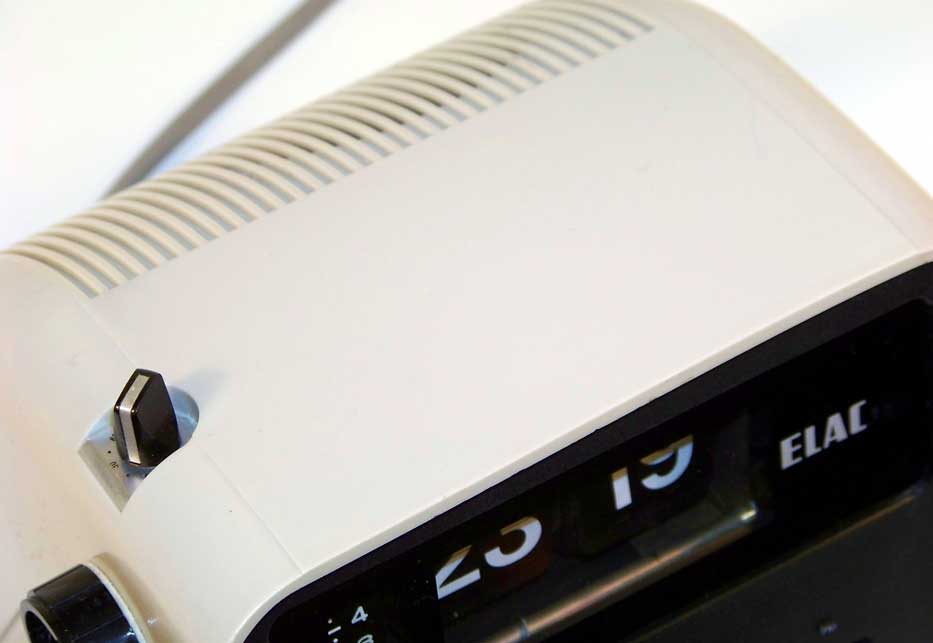
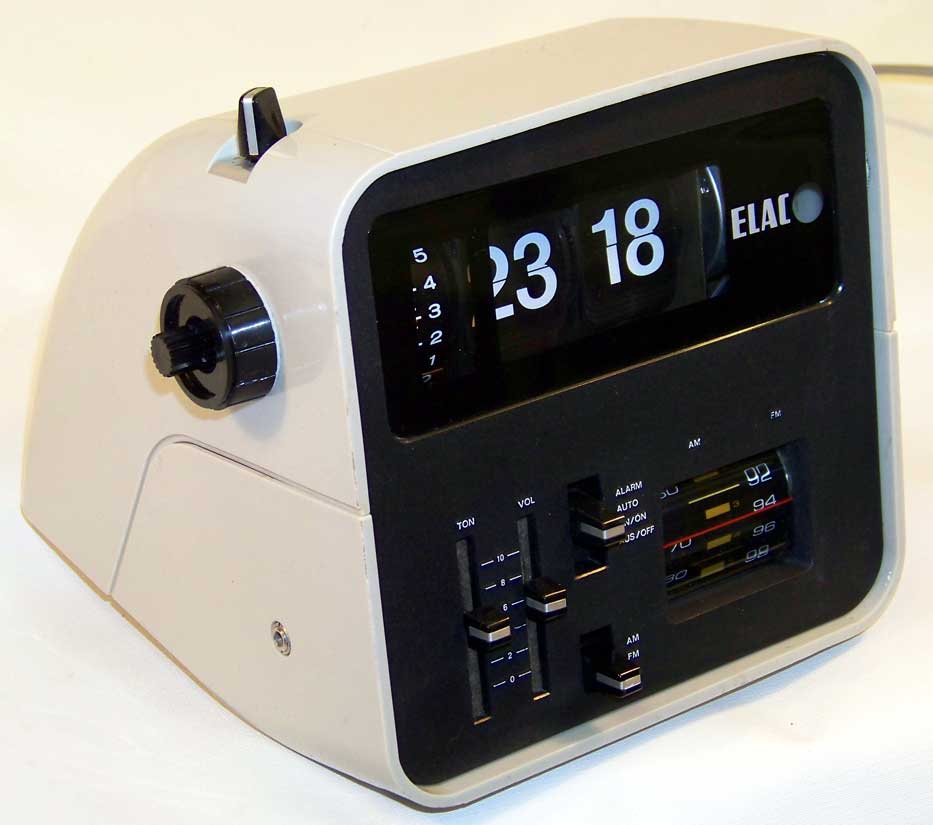
Rüdiger Walz
Für diesen Post bedanken, weil hilfreich und/oder fachlich fundiert.