Making a new brass (metal) badge or logo
Making a new brass (metal) badge or logo
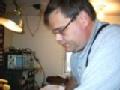
Making a new brass (metal) badge or logo.
I was working on the cabinet of a Philips table radio. The finish was in horrible shape. It appeared that some one may have used it to hold up their car while changing a flat tire. So, off with the old finish. In the process of stripping, the brass PHILIPS badge was damaged. Several letters became brass dust. The hunt for a replacement badge starts.
I searched the world over and did not find any brass PHILIPS badges. I emailed many contacts in the US, GB and Europe. No luck. Some fabricators could water jet or LASER cut one from brass. But WOW the cost. A couple hundred dollars in one case. I tried to make one myself.
First I tried to hand cut the lettering out of foil and a razor knife. Forget that. I do not have a steady hand. I found a silk screen photo exposure process. I sent my art work, $20 and receive a very fine detailed silkscreen mask. But I could not get a crisp paint image on lacquered surface.
Then I was reading a Micro-Mark catalogue. They sell supplies and tools for modeling. They carry a photo etching process to make 3D metal objects. Oh Boy! That’s it! I read the instructions on line then ordered a kit. Many technicians already have this set up to make Printed Circuit boards. I anticipated its arrival.
Micro-Mark Pro-Etch Photo Etch System
This picture is from the Micro-mark Catalogue
The first step it to create the art work. “Franklin Gothic Heavy” font in Microsoft Word matched perfectly. Then with the “Character Spacing” and “Spacing” under “Font” I matched the original character positioning.
This is the origonal Microsoft Word file. It has all the font and spacing adjustments. I hope they display for you when you open it on your computer.
To create the bar use “Underscore” with additional blank spaces. The bar was created under the letters.
The photo sensitive emulsion that is laminated onto the brass hardens when exposed to UV light. Therefore, the font has to be clear (white) with a black background.
A back rectangle was created and placed under the lettering. The lettering color is changed to white. This prints clear on the Ink Jet transparency that is included with the Micro-Mark etching kit.
Additional vertical lines were placed from the bottom of each character to the underscore bar. This attaches each letter to the bar as is with the original badge. Use Word’s drawing functions for this.
This is bare brass. There is no fiberglass backing board to protect the underside of the metal. So a mirror image has to be created and registered to the right reading image. This is properly explained in the instructions.
Microsoft word does not mirror fonts or images, at least not that I am aware. So I copied the image to Microsoft Power Point. Power Point has all the tools needed to work accurately with this image. It has a ruler, mirror and flip. I find it convenient, compatible with MSword and easy to work with. Follow the directions in the instructions on setting up your printer. I used HP Transparency with “Best” print quality on my HP F4180. It takes a while for the ink to dry. Be patient. On to the UV sensitive materials.
The Micro-Mark instructions are quite detailed and complete. I will not try to re-explain them here.
I created a dark room out of my shop by blocking windows with cardboard and using two 60 watt 130 volt yellow bug lamps. This is not necessary but I wanted the extra time to carefully work with the photo-sensitive material. Now that I have done this once I probably will only use a darkened room in the future.
After you have made the artwork and printed the Ink Jet sheets (included in kit) the general procedures:
i
Cut the photo sensitive resist material to cover the front and back. This is the photo sensitive material. I used a Dark Room environment to increase my work time. I do not have a photo of this material.
Laminate the photo resist material to the brass.
Clamp the mask (created with the printer) to the prepared brass plate between the provided Plexiglas.
Expose the photo resist. I used direct sun light at 3pm and 30 seconds exposure per side (front and back).
Develop the photo resist. Safe light is no longer needed after developing the photo resist. This is the plate after developing in Sodium Hydroxide solution. The blue letters is the hardened and developed Photo Resist material that has been exposed to the Sun.
I inked in the black with a Sharpie. The letters would drop off into the tank of acid if there was no support structure. The badge will be clipped off after water rinse.
Etch the brass plate to remove unneeded material.
Tank with bubbler in bottom and brass submerged.
After about 5 minutes etch time above.
About 10 minutes above three images.
About 15 minuits for the above three pictures. You can see the two different fonts. One is bold. I started etching at 5 past the hour.
After water rinse. The blue color is the hard photo resist. A bath of undiluted Sodium Hydroxide removes this resist material.
Remove the hardened photo resist material and polish your new brass badge.
Look in amazement at your creation.
Glue with contact cement to the refinished radio cabinet and overcoat with lacquer.
I am still impressed with the detail and accuracy of this process. Non continental US customers can purchase this kit without the two chemical. These chemicals are to be purchased local to you.
You may be able to assemble this kit individually. However, I am so impressed by the results and ease of use that I highly recommend purchasing this kit. Those of you that have a PC etching set up probably will not need this complete kit. Feel free to download and use my Microsoft “PHILIPS” files for your personal non-commercial use.
This is the radio being restored. I will post final pictures when available.
Good luck and post your experiences here.
Paul Pinyot.
Attachments:To thank the Author because you find the post helpful or well done.